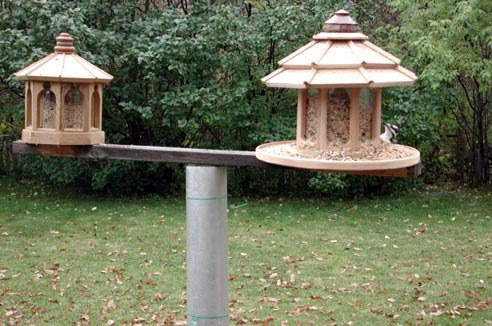
It looks like I managed to get pictures in here so here goes the story:
BTW, that is a Downey woodpecker doing a close up investigation.
I have been fussing with critters all my life and birds are among my favourites.
By attracting them I gain the benefit of their company and the side benefit of their constant insect control.
These feeders are 8 sided and fun to build in the shop.
I have found some work arounds for the windows and the feed area that could save you some time.
I like to keep a piece of cut stock from a previous feeder to use as a guide to set up my saw
For future cuts but I am finding that this wixey angle gauge is taking a lot of the set up time out of the job.
Now I just set the angle off the number of segments and let the Wixey figure out the compound angle for the saw.
Here's how it works:
1.Take the angle off an old segment as I do here or calculate it from a table.
there are numerous on the net and some in Excel if you prefer.
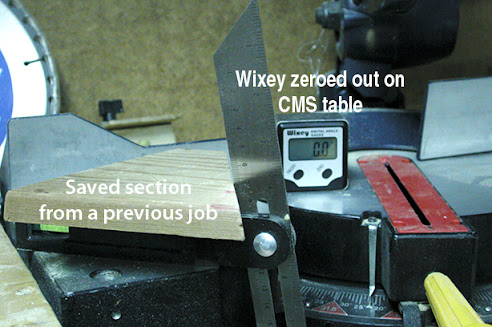
2. Set the Wixey on the saw table and zero it out.
3. Using a steel miter gauge set the Wixey on it a measure the angle difference vs the table and the gauge.
Transfer the Wixey to your saw blade and set in the same angle you got from the bevel gauge.
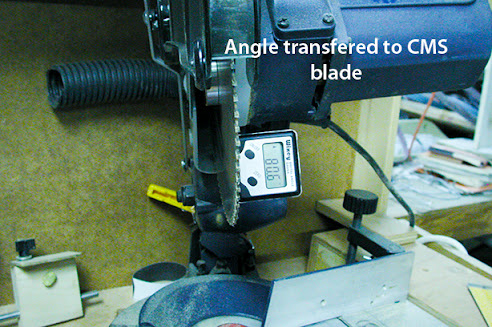
The diameter of your roof will vary with the stock you choose but the angle of slope will remain the same.
4. Saw up 4 pieces and set them with masking tape against a flat board and check your fit.
Adjust if necessary.
If they are a fit, cut the other 4 pieces and get ready to glue them.
You pretty much should use polyurethane glue ( Elmers or Gorilla for example) to get a weather proof seal as Most of the joints are end grain and will be sitting in moisture alot.
Wear gloves with this Stuff, it stains your hands.
Use it sparingly and spray the glued surface with water to hasten the cure.
I apply the glue on one surface and wet the mating surface.
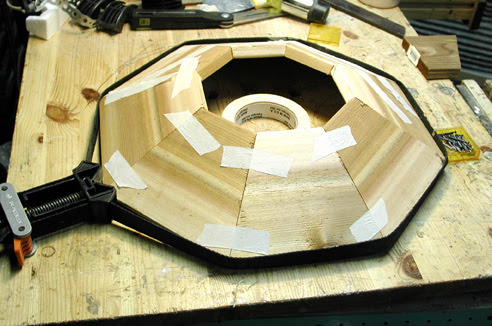
to be continued...