and"Anant tools":
etc.
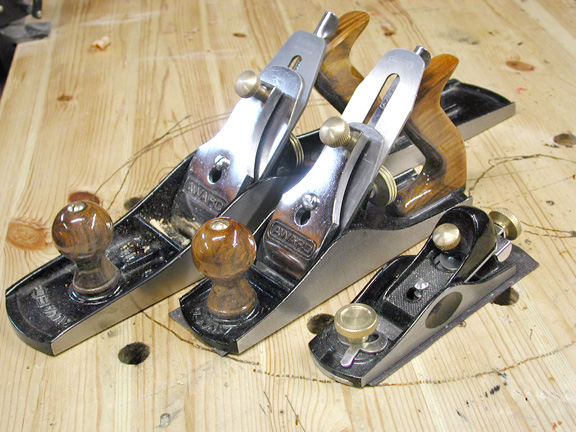
I purchased these three planes at a local store here for from $15.00 to $40 each.
Having attempted to restore several old Bailey's and Sargents and Stanley's I found that
lately the prices on E-bay for vintage tools has been tarnished by extremely high shipping costs and the inevitible "padding" of the price by shady merchants. And to be quite honest, in my opinion, they were not made all that well in the first place. (Your milage may vary)
Right out of the box, these all performed much better than my expectations and required no adjustment of the plane bases and or blade fittings. The castings, seem of very high quality, and did not require any adjustment.
I sharpened the blade in the No.6 plane (18" long), and used it on several different species of wood and was impressed with how well it cut.
I was curious to find out what improvement a *high end blade* would make with this plane so I ordered a new blade from Lee Valley made from A2 steel.
As you may know, A2 steel is much harder than 01 carbon steel and although more difficult to sharpen it keeps an edge longer. I have a "Worksharp, sharpening system ":http://lumberjocks.com/jocks/boboswin/blog/2399 so I was not too concerned about the extra work in sharpening this type of blade. As shown in the picture the Lee Valley blade is considerably thicker than the original. Lee Valley claims this extra thickness helps prevent chatter from the blade.
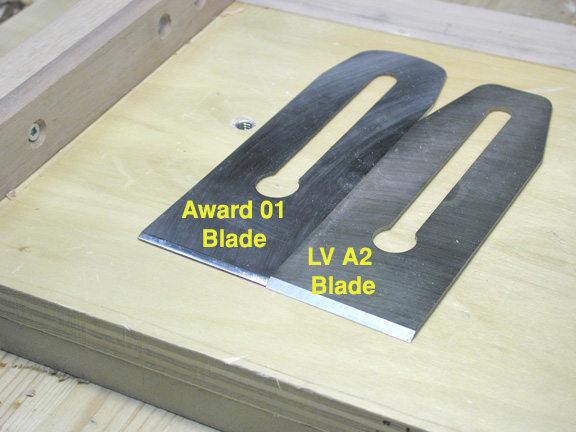
Next I removed the blade and chip breaker and gently filed the frog so that it was continuous with the angle formed in the sole of the plane. It went fairly quickly, as there was negligible material that needed to be removed.

Next, I set out my sharpening station and set the blade angle to 25° using the wixey gauge to get an accurate angle.
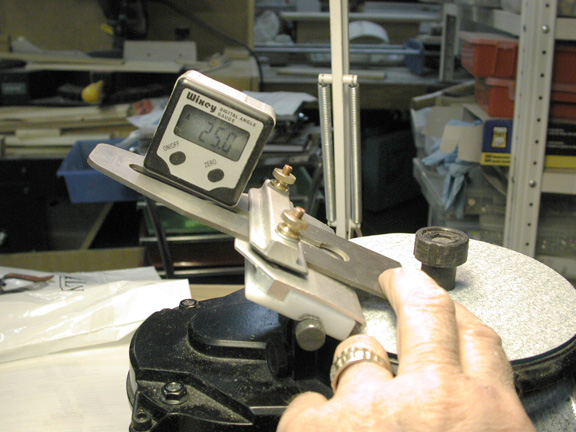
The next shot shows the blade, as it comes off the Worksharp system.
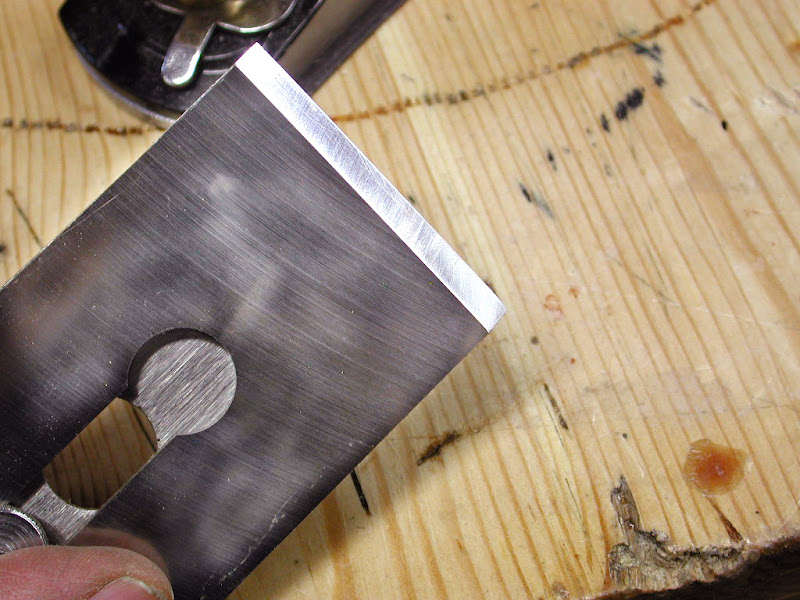
I reassembled my plane and tested it out with a handy stick on the shooting board. The new blade got noticeably smoother than the original and the additional thickness narrowed the mouth of the plane leaving just enough room for those fine shavings to exit.

I'm very satisfied with this modification to the original plane and hope to modify the other two in the weeks to come. I will admit that the new blades actually cost more than the original plane. But all in all, it turns out to be very good value.
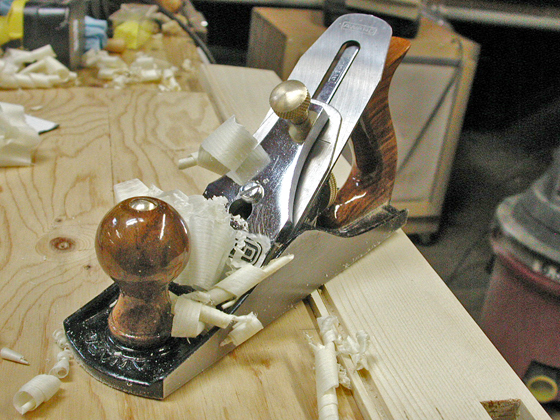
I am the first to admit that they are not the same quality as a Lee Valley or a Lie Neilson but they will certianly do until I win the next lotto.